Зачем бизнесу цифровизация: опыт НЛМК
Григорий Федоришин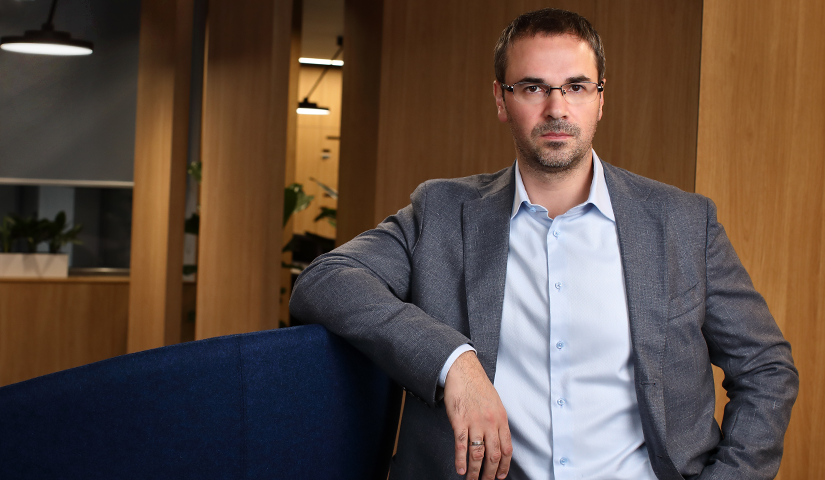
От редакции. По просьбе renchen.ru президент НЛМК Григорий Федоришин рассказал об опыте цифровизации металлургического бизнеса и объяснил, почему компаниям не стоит бездумно гнаться за технологиями.
Группу НЛМК я возглавил в 2018 году, но мое видение цифровизации компании осталось неизменным. Я отношусь к новым технологиям прагматично — как к инструменту достижения стратегических целей. Я никогда не рассматривал цифровизацию как самоцель и пытался понять, какой именно результат мы получим. Основной стратегический фокус НЛМК — операционная эффективность, устойчивое развитие и безопасность. Если цифровизация помогает в этом — отлично, если нет, значит, она лишь красивая игрушка, которая нам не нужна.
Реализовав стратегию НЛМК на период 2013—2017 гг., мы структурно увеличили финансовый результат более чем на $1 млрд в год. Из этого эффекта почти $700 млн мы получили благодаря повышению операционной эффективности производства и вспомогательных процессов. Наши сотрудники реализовали несколько тысяч проектов и инициатив. Соответственно, мы в какой-то степени исчерпали возможности базовых инструментов бережливого производства. Чтобы наращивать эффективность высокими темпами, нужно внедрять более сложные инструменты.
В ближайшие пять лет мы планируем увеличить отдачу от проектов, связанных с операционной эффективностью, еще на $500 млн в год. И рассматриваем цифровизацию как один из доступных инструментов с хорошим потенциалом для достижения цели. Внедрить новые технологии в производственную цепочку не так сложно, гораздо труднее интегрировать их в повседневную работу сотрудников. За последние два года мы попробовали разные варианты, совершили свои ошибки и поняли, что главное — не технологии, а люди.
СТАЛЬНОЙ ГИГАНТ
Группа НЛМК — международный производитель стали с вертикально-интегрированной моделью бизнеса. Флагманский актив — Новолипецкий металлургический комбинат. Компания состоит из шести дивизионов: «Плоский прокат РФ», «Руда», «Сортовой прокат РФ», «Толстый лист Европа», «Плоский прокат Европа» и «НЛМК США», которые составляют производственную цепочку от добычи сырья до выпуска металлопродукции с высокой добавленной стоимостью. Компания является крупнейшим производителем стали в России: в 2018 году она произвела 17,5 млн тонн стали, выручка составила $12 млрд, чистая прибыль — $2,2 млрд.Первый цифровой опыт
НЛМК давно и активно использует информационные технологии, просто раньше никто не называл автоматизацию производства цифровизацией. Это как с человеком, который не догадывался, что всю жизнь говорил прозой. Автоматика и сложные системы управления стали частью металлургического производства несколько десятков лет назад. Новая волна сбора и использования данных началась относительно недавно — она вызвана внедрением инструментов бережливого производства, которые требуют применения статистических методов.
Компания генерирует огромное количество данных, только они связаны не с клиентами, как у банков или ритейла, а с различными физическими и химическими показателями процессов. Эту информацию можно обрабатывать и использовать ее для повышения эффективности производства и повышения качества конечного продукта. Поэтому два года назад в группе НЛМК появились специалисты по большим данным и математическому моделированию, мы создали центр цифровых компетенций и запустили несколько пилотных проектов.
Через некоторое время мы заметили, что часть проектов успешно завершаются, мы видим красивые отчеты, но потом эти начинания тихо «умирают». Мы стали анализировать причины и поняли, что производственные подразделения часто не понимают, зачем им нужны эти новации. А если понимают цель, то не всегда верят в реальную пользу, зато четко видят риски. Например, у мастера появился электронный советчик, который рекомендует оптимальный выбор в той или иной ситуации, например, в какой пропорции смешать сырье. Однако ответственность за результат несет мастер, а не «советчик». Цена ошибки в реальном производстве высока, как можно довериться математической модели? Еще сложнее принять такой совет, когда ты не понимаешь, по какому принципу работает «черный ящик» алгоритма, какие закономерности учитывает. В результате мастер говорит: «Отлично, спасибо!» — и продолжает работать так, как считает нужным.
То есть некоторые наши эксперименты оказались не связаны с потребностями бизнеса и жили отдельной жизнью. Мы думали в первую очередь о технических инструментах (больших данных, датчиках, искусственном интеллекте и т. п.), а не о реальных потребностях производства. Очевидно, нужно было действовать по-другому.
Мы кардинально пересмотрели прежний подход и стали создавать смешанные, или, как мы их называем, «продуктовые» команды, в которые включили производственников, технологов, специалистов по ИТ и работе с данными. При этом руководили ими именно люди с операционным опытом -– начальники производственных участков или опытные мастера.
Работа команд началась с того, что производственников попросили обозначить свои проблемы и пожелания — у кого что «болит», кому что нужно для собственных планов. В НЛМК у всех сотрудников есть цели, которые связаны с нашей стратегией. Например, мы понимаем, как через пять лет должен работать конкретный прокатный стан, каким должно быть качество выпускаемой продукции, расход сырья, время простоев и т. д., чтобы стратегия в этой части была выполнена. И каждая бригада, которая работает с конкретным агрегатом, знает, каких результатов она должна добиться. Конечно, достичь этих целевых показателей непросто, иначе все компании были бы одинаково эффективными и прибыльными. Поэтому производственный персонал с готовностью откликается, если ему предлагают помощь в решении конкретных задач.
Команды обсуждают, в каких проблемных или высокопотенциальных направлениях могут помочь цифровые инструменты, формулируют гипотезы, как это можно сделать. Сейчас у нас десять таких команд на разных площадках, они объединяют более 100 человек. Специалисты разных подразделений вместе работают над математическими моделями и прототипами и тут же на производстве их тестируют. Здесь важны вовлеченность и скорость. Когда презентуются результаты проектов, это делают сами начальники цехов — они рассказывают, как инструмент помогает им повышать операционную эффективность.
В итоге производственные подразделения приняли идею, что совместная работа направлена на решение их задач, увидели потенциал в цифровых технологиях. Мы также дали людям возможность ошибаться. Не все проекты принесли отдачу, но общий технический и финансовый эффект, безусловно, положительный.
Завод на ладони
