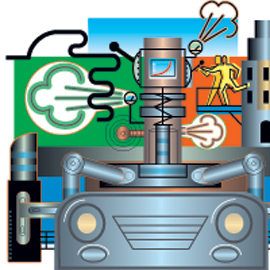
читайте также
Toyota – одна из самых именитых компаний в мире. Она из года в год опережает конкурентов по таким показателям, как качество, надежность, производительность, объем продаж, минимизация издержек, рост рыночной доли и капитализации. В конце прошлого года Toyota чуть было не обошла входящую в “большую тройку” DaimlerChrysler, почти догнав ее не только по объему продаж, но и по объему производства. По доле на мировом автомобильном рынке она недавно опередила Ford и заняла второе место, а по объему чистой прибыли и рыночной капитализации (данные на конец 2003 года) вышла на первое место. Секреты высокой эффективности японской корпорации пытаются разгадать руководители бизнеса, аналитики и журналисты. Возникает вопрос: если все так тщательно изучают и копируют методы Toyota, то почему мы почти не встречаем компаний, сумевших сравняться с ней по эффективности?
Несколько лет назад мы с Кентом Бауэном опубликовали статью “Расшифровка ДНК-кода производственной системы Toyota” (Decoding the DNA of the Toyota Production System, HBR, сентябрь – октябрь, 1999). В ней говорилось, что подражатели стремятся скопировать прежде всего конкретные методы и инструменты Toyota (например, карточки канбан или производственные ячейки), вместо того чтобы перенять и освоить базовые организационные принципы. Нам удалось выявить четыре принципа, лежащие в основе производственной системы корпорации, которые создают условия для постоянного повышения надежности, гибкости, безопасности, эффективности производства и в итоге – рыночной доли и прибыльности компании.
Мы старались показать, что главное достижение Toyota не в создании и внедрении инструментов как таковых, а в превращении всей производственной деятельности в цепочку экспериментов, встроенных в рабочий процесс. Эксперименты проводятся на всех его этапах и уровнях – от самых простых операций (типа установки автомобильных сидений) до самых сложных и масштабных (вроде запуска новой модели или даже нового завода). Всем известное стремление Toyota к стандартизации, говорилось в нашей статье, направлено не на усовершенствование контроля и даже не на воспроизведение “лучшей практики”. В Toyota скрупулезное следование предписаниям сочетается с экспериментированием в процессе работы. Такой подход позволяет немедленно, прямо в ходе эксперимента понять, в чем состоит проблема. При этом удается более глубоко изучить производимый продукт, а также производственный процесс и его участников, после чего формируется новое предписание, которое становится “лучшей практикой” – естественно, до тех пор, пока не обнаружатся новые проблемы (см. «Сила принципов»).
Итак, производственная система Toyota (Toyota Production System, TPS) представляет собой цепочку включенных в рабочий процесс экспериментов. Но одно дело – понимать это, и совсем другое – руководить организацией, в которой сотрудники на всех уровнях и участках должны применять принципы деятельности Toyota и обучать этому других.
Посмотрим, как приобщался к таинству TPS молодой американский менеджер – назовем его Боб Дэллис, – получивший высокий пост на одном из заводов Toyota в США. Его путь к цели оказался неожиданно трудным и длинным. Получив блестящее образование (даже не в одном, а в двух престижных университетах), Дэллис до устройства в Toyota успел поработать на руководящих должностях в другой крупной автомобилестроительной компании, а потому можно было ожидать, что стажировка в японской корпорации займет не слишком много времени. Но вышло иначе: Боб постигал TPS медленно, досконально вникая во все детали системы и используя усвоенные принципы на практике. Прошло более трех месяцев, прежде чем Дэллис попал на завод, где ему предстояло занять одну из руководящих должностей. Такой путь в Toyota проходят все новые сотрудники, независимо от должности и специализации.
Между тем Дэллис пришел в компанию, полагая, что уже знаком с принципами TPS (он почерпнул некоторые сведения на предыдущей работе) и ему достаточно лишь немного отшлифовать имеющиеся знания, чтобы приступить к оптимизации производства на новом месте. По окончании подготовительного периода Дэллис понял, что оптимизация конкретных операций вовсе не его дело – этим должны заниматься сами рабочие; его же обязанность – помочь подчиненным осознать, в чем состоит их задача, и научить решать ее. В процессе стажировки он овладел искусством выстраивать свою работу в виде системы экспериментов – этот процесс подразумевает непрерывное самообучение и самосовершенствование, а также передачу накопленных знаний и наработанных методов другим людям.
Стажировка
В январе 2002 года Дэллис прибыл в офис Toyota в Кентукки. Его встретил Майк Такахаси (имя изменено), один из руководителей Центра поддержки поставщиков Toyota (TSSC). Эта структура отвечает за обучение основам TPS сотрудников предприятий самой Toyota и ее партнеров-поставщиков, и на Такахаси была возложена задача подготовить Дэллиса к работе в компании. По завершении необходимых формальностей Такахаси усадил подопечного в свою машину и повез на завод – но не на тот, где Бобу предстояло занять руководящую должность. Новый сотрудник должен был начать свое вхождение в корпоративную структуру на другом заводе Toyota. Интенсивная стажировка там заняла 12 недель, затем последовала 10-дневная ознакомительная работа на предприятиях Toyota и ее поставщиков в Японии.
Назад, к основам. Первое задание, которое получил Дэллис на американском заводе Toyota по производству двигателей, состояло в том, чтобы помочь группе из 19 рабочих сборочного цеха повысить производительность, эксплуатационную готовность оборудования1 и безопасность труда. Первые шесть недель Дэллис под руководством Такахаси наблюдал за работой отдельных сборщиков и предлагал варианты усовершенствований, уделяя особое внимание повышению производительности и безопасности. Работая с руководителями групп и бригад, а также с рядовыми исполнителями, Дэллис вел журнал – записывал, как осуществлялись те или иные операции, кто и при каких обстоятельствах выполнял задания, как проходил обмен информацией и материалами, как участники процесса взаимодействовали друг с другом. Для решения выявленных проблем он предлагал свои варианты изменений, а затем оценивал результат.
К началу стажировки Дэллис уже обладал определенным опытом, тем не менее каждая рабочая неделя начиналась и заканчивалась встречей с наставником. В понедельник Дэллис должен был изложить Такахаси свое понимание работы сборочного цеха, основанное на наблюдениях предыдущей недели, перечислить замеченные проблемы и меры, которые он и его сотрудники приняли или намерены принять для их решения, а также оценить возможный эффект от этих мер. В пятницу Такахаси анализировал сделанное Дэллисом и сравнивал результаты с планами, намеченными в понедельник.
За первые пять недель в отдельные сборочные операции было внесено 25 усовершенствований. Например, работники цеха переставили несколько стоек с комплектующими, сделав доступ к ним более удобным, а у одного из механизмов было решено переместить рычаг – это снизило нагрузку на кисть руки оператора и повысило безопасность работы. Кроме того, Дэллис и другие участники группы внесли 75 предложений, касавшихся распределения работы. Изменения были весьма значительными и потребовали перепланировки цехового пространства. К примеру, чтобы перенести место монтажа одного из узлов, пришлось реорганизовать складскую систему, переместить шторки безопасности и внести изменения в схемы проводок и сервисные компьютерные программы. Всю эту работу специалистам из отделов технической и инженерной поддержки приходилось делать в выходные.
Шестая неделя была посвящена анализу результатов 75 произведенных изменений. Перемены действительно привели к значительному повышению производительности и безопасности труда в сборочном цехе (см. «Сборочная линия: до и после»). К тому же на участке, где раньше трудились 19 человек, усовершенствования Дэллиса позволили сократить число рабочих до 15. К сожалению, одновременно с этим снизилась эксплуатационная готовность оборудования цеха. Раньше, до перемещений, последовательность операций была выстроена так, что сбой на одном участке обычно не оказывал непосредственного влияния на работу смежников. Теперь, когда система стала более четкой и компактной, сбои превратились в серьезную помеху.
После того как Дэллис добился улучшения работы персонала цеха, Такахаси велел ему переключиться на изучение работы оборудования. Эта фаза заняла еще шесть недель, причем Дэллис и Такахаси по-прежнему встречались по понедельникам и пятницам. Стажер с двумя дипломами о высшем техническом образовании должен был внимательно наблюдать за функционированием механизмов, а при возникновении сбоя – тут же определять причину. Это оказалось непросто: сбои, обусловленные действиями людей, происходили едва ли не каждые 30 секунд, что давало богатый материал для анализа, в то время как неполадки оборудования случались гораздо реже и их причины обычно были скрыты внутри машин.
Вскоре Дэллис стал замечать, что очень часто сбои объяснялись особенностями взаимодействия человека с машиной. К примеру, поместив инструмент в зажим, нужно установить зажим в станок, после чего запустить операцию, но иногда один из рабочих переключал рычаг станка прежде, чем зажим встанет на место. Определив причину сбоя, Дэллис попросил специалистов из службы технической поддержки переместить рычаг. В другой раз, проанализировав ряд повторявшихся сбоев, Дэллис понял, что поддон наталкивается на ограничитель, расположенный внутри машины. Эту проблему тоже удалось решить: неудобный ограничитель заменили на аналогичную деталь с другим профилем сечения.
Наблюдая за работой устройств, выявляя причины возникавших неполадок и оперативно модифицируя проблемные узлы, Дэллис сумел восстановить исходный уровень эксплуатационной готовности оборудования, снизившийся на предыдущем этапе. Однако довести ее до 95% (именно эту цель поставил перед стажером Такахаси) так и не удалось.
Мастер-класс. После того как Дэллис провел на американском заводе Toyota 12 недель, Такахаси счел, что новый сотрудник овладел искусством наблюдения за людьми и машинами и научился решать проблемы, ставя серии экспериментов. Вместе с тем наставника беспокоило, что Дэллис многое делает самостоятельно, не подключая рабочих, и слишком долго тестирует нововведения.
Такахаси решил, что пора показать стажеру, как Toyota осуществляет усовершенствования на родной земле, и они полетели в Японию. Первые три дня Дэллис должен был провести на знаменитом заводе по производству двигателей в Камиго, в том самом месте, где Тайити Оно, один из создателей TPS, разработал и внедрил свои знаменитые инновации. В день прибытия Такахаси преподнес своему подопечному первый сюрприз: наблюдая за рабочим одной из производственных ячеек, Дэллис должен был сделать 50 усовершенствований. На каждое усовершенствование, таким образом, отводилось всего 22 минуты, а не целый рабочий день, как раньше.
Изначально перед Дэллисом была поставлена задача снизить нагрузку на рабочего – уменьшить количество перемещений и движений, не увеличивающих стоимости продукта, утомляющих оператора и удлиняющих операционный цикл. Такая формулировка задачи неслучайна: фокусирование на снижении нагрузки означало, что надо оптимизировать рабочий процесс. Если бы речь шла о сокращении потерь времени, то подразумевалось бы, что проблема в человеке.
На новом месте Дэллис использовал принципы, усвоенные на заводе в США. В первый день он потратил три часа, наблюдая за напарником. К концу смены он с гордостью доложил, что у него появилось семь идей и четыре из них уже реализованы. И тут Такахаси преподнес второй сюрприз, сообщив, что два японских стажера, претендующих на менее значительные должности, чем Дэллис, за то же время успели сделать гораздо больше: один из них внес 28 рацпредложений, другой – 31. Дэллис постарался ускорить поиски возможностей для оптимизации, перейдя на более быстрые и “грязные” методы тестирования: сварку заменяли болтовым креплением, вместо крепления болтом использовали веревку, а то и без нее обходились – просто поддерживали деталь руками. Словом, делали все, чтобы быстрее увидеть результаты изменений. К утру второго дня Дэллис с напарником подготовили список уже из 25 идей. Такахаси время от времени заходил в цех, спрашивал, что Дэллис обдумывает в данный момент, задавал очень детальные вопросы. “Прежде чем я успевал что-либо объяснить, – вспоминает Дэллис, – он отправлял меня проверить изменение на практике”.
Стажер убедился, что теперь он куда быстрее обнаруживает и решает проблемы. Утром третьего дня он смог перейти от изучения отдельных операций к анализу организации производственной ячейки в целом. “На участке были две машины, оснащенные приборными панелями, а также стойки с комплектующими, – рассказывает Дэллис. – В одном случае для замены инструмента требовалось восемь шагов, в другом – двадцать четыре. Я подумал: а нельзя ли изменить компоновку оборудования так, чтобы сократить число шагов, а значит, и время выполнения операции? Мы сумели смоделировать изменение, не прибегая к перестановке тяжелых машин”.
К концу третьего дня Дэллис выявил 50 недоработок в системе контроля качества, в схеме замены инструментов и прочих составляющих производственного процесса, причем 35 проблем удалось устранить сразу же. Стажер тщательно фиксировал в журнале произведенные изменения и их результаты (см. «Усовершенствования на заводе в Камиго»). Отражались замеченные проблемы, способы устранения каждой из них, результаты усовершенствований, а также отношение рабочих к принятым мерам (см. «Выдержки из журнала Дэллиса»). Описания сопровождались фотографиями и диаграммами.
По завершении этого этапа Такахаси представил результаты работы Дэллиса управляющему завода, начальнику цеха и цеховым мастерам. “Руководители активно участвовали в обсуждении, – говорит Дэллис. – Большинство присутствовавших делали пометки и подробно расспрашивали выступавших”.
В оставшиеся дни Такахаси показывал Дэллису, как цеховые мастера Toyota реализуют свои рационализаторские проекты и отчитываются о них. Каждый бригадир излагал суть проблемы, описывал способ ее решения и эффект от произведенного изменения. Дэллис увидел, что от руководителей всех уровней здесь требуется умение организовать работу и постоянно проводить эксперименты с целью усовершенствования производственного процесса.
Уроки
Такахаси ни разу не сказал своему подопечному, что именно ему необходимо усвоить, но методика проведения стажировки позволила Дэллису определить, по меньшей мере, четыре основополагающих принципа, на которых строится производственная система компании.
Урок 1: Ничто не заменит непосредственного наблюдения
В течение всего времени стажировки Дэллису вменялось в обязанность внимательно наблюдать за работой людей и механизмов. При этом исключались какие бы то ни было умозрительные предположения о причинах сбоев – требовалось в деталях изучить ситуацию в момент неполадки и визуально определить, в чем причина и что необходимо сделать.
Эта идея была наглядно представлена в отчете одного из мастеров на заводе в Камиго. Речь шла об оптимизации обслуживания механизма. Оказалось, что причину неполадки оборудования можно выяснить только в момент сбоя. Мастер велел снять с машины кожух, чтобы бригадиры и рабочие могли видеть и слышать, что происходит внутри, оценивать состояние механизма в процессе операции и прогнозировать надвигающийся сбой. Этот подход в корне отличается от используемых в большинстве компаний методов опосредованного анализа, которые основываются на отчетах, беседах, обзорах, статистике, сводных данных и т. п. Действительно, такие методы позволяют увидеть общую картину; тем не менее непосредственное наблюдение необходимо, его не заменишь никакими хитроумными сочетаниями приемов опосредованного анализа.
Благодаря своему опыту управления производством Дэл-лис умел видеть проблемы в целом. Но если бы Такахаси поручил стажеру более масштабную задачу, тот не научился бы с таким вниманием подходить к деталям. За шесть недель стажировки на американском заводе Дэллис мог наблюдать за полным операционным циклом 23 824 раза – по тысяче с лишним на каждого из 19 рабочих. Это позволило ему досконально разобраться во всех проблемах, имеющих отношение к производительности и безопасности сборочного участка.
Урок 2: Изменения вводятся в режиме эксперимента
В науке эксперименты проводят для проверки правильности гипотез: полученный результат позволяет либо уточнить гипотезу, либо отказаться от нее.
Сталкиваясь с той или иной проблемой на производстве, многие выдвигают гипотезы о ее причине и идеи относительно возможного решения. Но TPS подразумевает нечто большее: от человека требуется глубокое понимание сути проблемы и умение ее решить. В принципе, любой менеджер может сказать: “Пожалуй, эту стойку с запчастями нужно придвинуть ближе к оператору. Наверняка мы таким образом сократим операционный цикл на несколько секунд”. Если он проверит эту мысль на практике и сэкономит в результате шесть секунд, он будет вполне удовлетворен и сочтет, что проблема решена.
Однако, с точки зрения менеджера корпорации Toyota, такой результат говорит о том, что человек не до конца разобрался в сути работы, которую пытается оптимизировать. Почему он не конкретизировал, как далеко нужно переместить стойку? Сколько именно секунд он планировал сэкономить? Скажем, если ожидалась экономия в четыре секунды, то полученные шесть секунд – не только очень серьезный успех, но и повод для дальнейшего исследования. Такой подход требует конкретности и точности, и расхождение между прогнозом и результатом (откуда взялась разница в две секунды?) должно привести к более глубокому изучению производственного процесса, а главное – методики, в соответствии с которой менеджер исследует и оптимизирует процесс.
Урок 3: Как можно больше экспериментов
В Toyota считают, что лучше провести много быстрых и простых экспериментов, чем пару-тройку длительных и сложных. Дэллис понял это во время работы в Японии. В США он за шесть недель успел внедрить лишь 25 усовершенствований, а в Камиго ему пришлось реализовать 50 рацпредложений всего за две с половиной рабочие смены. Дэллис понял, что продвигаться маленькими шажками эффективнее, чем
затевать масштабное преобразование: он постоянно видел проблемные участки и результаты изменений, оперативно проверял свои догадки на практике. Именно так подходят к усовершенствованию производственных процессов работники Toyota. Они накапливают опыт в процессе наблюдения и экспериментирования, а не в момент внесения изменений. Такахаси выстраивал задачи для Дэллиса так, чтобы стажер получил необходимые навыки и вникал в суть проблем, причем сложность экспериментов постепенно возрастала. На первом этапе Дэллис занимался незначительными операциями с оптимизацией всего по одному параметру – говорить о масштабных, системных проектах было рано. Накопив за шесть недель первичный опыт наблюдения и решения проблем, Дэллис перешел от коррекции деятельности одного работника к более сложным и тонким задачам, связанным с функционированием механизмов. Когда обучение строится как последовательность простых, ограниченных задач, ошибки, которые может совершить стажер, не влекут за собой серьезных последствий. Не боясь ошибиться, обучаемый идет на риск и поэтому быстрее приобретает необходимые навыки. Подобная схема продвижения повторилась и на заводе в Камиго – там стажер начал с оптимизации нагрузки рабочих и лишь затем перешел к механизмам2.
Урок 4 Менеджер не решает проблемы, а учит этому других
Стажировка помогла Дэллису не только освоить методику непрерывного совершенствования производства в Toyota, но и понять, в чем состоит особенность отношений между менеджерами и рабочими корпорации. На прежнем месте работы руководство неоднократно поощряло Дэллиса за его умение решать проблемы. Но на предприятиях Toyota он, к своему удивлению, обнаружил, что решение проблем – обязанность рядовых рабочих и руководителей нижнего уровня: чем выше ранг менеджера, тем реже ему приходится заниматься этим самому.
Фактически задача менеджера Toyota – дать подчиненным возможность решать проблемы. Такахаси, один из топ-менеджеров корпорации, в процессе подготовки Дэллиса действовал не как технический специалист, а как учитель и наставник. Он помог подопечному пройти курс стажировки, не подсказывая в явном виде, чему тот должен научиться. Даже когда Такахаси обучал Дэллиса конкретным навыкам, он делал это лишь для того, чтобы стажер смог более эффективно экспериментировать. К примеру, однажды наставник показал ему, как наблюдать за действиями отдельных рабочих, чтобы подметить непродуктивные движения и признаки утомления, в другой раз дал совет, как строить экспериментальные модели. Но сам он не внес ни одного рационализаторского предложения, ограничиваясь лишь подсказками типа “Обрати внимание на этого человека” или “Посмотри, нет ли в его действиях напряжения, неловкости”.
Такахаси предоставлял стажеру все ресурсы, необходимые для повышения скорости работы. Например, на заводе в Ка-миго Дэллису был выделен напарник, помогавший передвигать оборудование, менять конфигурацию проводки, закреплять детали и т. д. Благодаря этому у стажера было больше времени на эксперименты. Кроме того, Такахаси и начальник цеха посещали участок, на котором Дэллис тестировал свои идеи, и помогали скорректировать планы до начала изменений. Когда Дэллис предложил модификацию измерительной секции, начальник цеха показал ему, как быстро и без затрат соорудить картонный прототип, на котором можно проверить оптимальность предлагаемых размеров, углов и т. д.
Такая необычная схема взаимоотношений между менеджерами и рабочими обеспечивает высочайшую продуктивность при решении сложных задач на всех уровнях производства. “Я, человек с опытом работы на заводе по производству двигателей, увидел в Камиго сборочную линию, пущенную 15 лет назад, но до сих пор успешно справляющуюся с изготовлением двигателей 90 различных типов, – вспоминает Дэллис. – Поразительно, как много усовершенствований им удается осуществлять с помощью простых средств. Каждое изменение было результатом очень глубокого осмысления проблемы”. Главная идея производственной политики Toyota состоит в том, что любую функционирующую систему можно усовершенствовать, если на каждом ее уровне сотрудники внимательно наблюдают и интенсивно экспериментируют. Всего за три месяца стажировки Дэллис научился тому, как помогать другим выдвигать и реализовы-вать рацпредложения. Возможно, в этом и состоит главный фактор успеха Toyota3.
Снова в Америке
Чтобы проверить, насколько Дэллис усвоил преподанные ему уроки, Такахаси вновь послал молодого специалиста на тот завод в США, где он начинал обучение. Как мы помним, стажер еще до поездки в Японию успел реализовать многие из своих идей, однако ему не удалось довести эксплуатационную готовность оборудования сборочной линии до намеченных 95%. Теперь наставник дал ему еще один шанс. Правда, на этот раз Дэллис понимал, что о прежней роли – человека, самостоятельно решающего проблемы, – ему придется забыть.
На новом этапе Дэллис при поддержке Такахаси работал вместе с мастером сборочной линии и его помощником, обучая бригадиров и рядовых рабочих решать проблемы, чтобы они сами могли устранять мелкие неполадки. При этом выяснилось, что бригаде трудно следить за ходом выполнения общей задачи и одновременно выявлять проблемы по мере их возникновения. Следовало усовершенствовать “визуальное управление” рабочим процессом, научиться определять, что идет хорошо, а где необходима коррекция и какая именно. Дэллис посовещался с мастером и его помощником, и они вместе составили график работы по выявлению проблем и распределили, кто за что отвечает. Члены бригады приступили к наблюдениям и поиску решений проблем, Дэллис заходил к ним (точно так же, как три месяца назад к нему заходил Такахаси), задавал вопросы и помогал таким образом выявлять проблемы. Результат превзошел ожидания: эксплуатационная готовность оборудования поднялась до 99%.
Три месяца стажировки кардинально изменили представления Дэллиса о месте менеджера в производственном процессе. Наблюдая за тем, как руководит его подготовкой Такахаси и как проходит стажировка других специалистов, Дэл-лис понял, что топ-менеджеры не должны заниматься непосредственным устранением сбоев, их задача - формировать команды первоклассных руководителей, способных учиться путем непрерывного экспериментирования. Формально после возвращения речь шла о той же цели, что и прежде, - доведении эксплуатационной готовности оборудования до 95%, но теперь он знал, что эта цель поставлена вовсе не перед ним.
И только тогда Такахаси счел свою задачу выполненной и допустил Дэллиса к работе, предусмотренной контрактом.
***
Возможно, стажировка в режиме полного погружения -вроде той, которую прошел Дэллис, - единственный способ понять, как действует производственная система Toyota, и тем более научиться совершенствовать ее. Кроме того, важно помнить, что любой человек, приходящий в Toyota извне, попадает в компанию, имеющую богатейший опыт оптимизации и рационализации. Темпы внедрения усовершенствований здесь чрезвычайно высоки - большинство других организаций могут об этом только мечтать. Маловероятно, что кому-нибудь удастся в течение нескольких недель и даже месяцев постигнуть, а тем более воссоздать эту мощную и своеобразную культуру. И все же, думаю, любая компания получила бы огромные преимущества, если бы разработала и внедрила у себя программу подготовки специалистов, подобную описанной в этой статье. Вы желаете воспроизвести ДНК-код TPS? Тогда рекомендую начать строить производственный процесс на основе принципов Toyota и наладить подготовку менеджеров, которые будут руководствоваться ими в своей работе.
1. Эксплуатационная готовность оборудования определяется соотношением времени полезного использования машины и общего времени ее работы. К примеру если на обработку поверхности детали требуется 8 минут, но из-за технических простоев полное время операции увеличивается до 10 минут, то эксплуатационная готовность оборудования - 80%. В идеальном случае она составляет 100%.
2. Пошаговое наращивание сложности облегчало работу и для Такахаси: он выстроил обучение Дэллиса в виде последовательности коротких циклов и непосредственно наблюдал за работой подопечного, регулярно оценивая успешность его продвижения. Благодаря такой обратной связи на каждом этапе он мог более эффективно определять задание для очередного цикла.
3. По словам Такахаси, на заводе в Камиго начальники, руководящие несколькими производственными ячейками, тратят около 70% своего времени на мероприятия, связанные с усовершенствованиями. Эти мероприятия обычно распределяются между тремя-четырьмя бригадами, так что каждый бригадир тратит на рационализацию примерно 20% своего времени.
Сила принципов
Для Toyota первичны основополагающие принципы, а не конкретные инструменты. Именно поэтому корпорация снова и снова оказывается впереди конкурентов. Многие пытались скопировать и применить методы Toyota, забывая о принципах. В результате возникала жесткая производственная система, которая на короткое время обеспечивала хорошие результаты, но испытания временем не выдерживала.
Понимание того, что суть TPS - это ее принципы, открывает компаниям, в том числе и совсем непохожим на Toyota, путь к долговременному успеху. К примеру, на предприятиях алюминиевого гиганта Alcoa производство ориентировано на непрерывные процессы - обогащение руды и выплавку металла. Казалось бы, здесь нет ничего общего с дискретным производством Toyota, где изготовляют детали и узлы, из которых затем собирают машины. Тем не менее производственная система Alcoa -Alcoa Business System (ABS) - базируется на принципах TPS. ABS позволила корпорации с 1998 по 2000 год сэкономить 1,1 млрд долларов, повысив производительность, безопасность и качество.
Есть примеры применения принципов TPS и в здравоохранении, например в Медицинском центре Питсбургского университета.