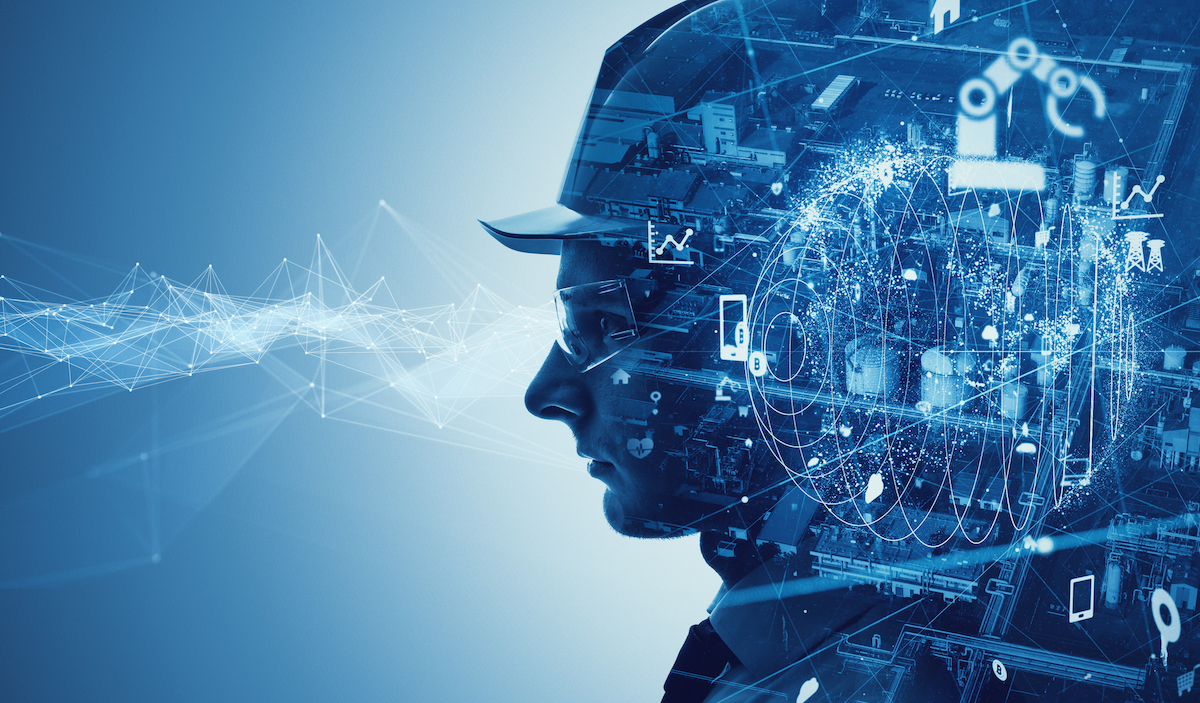
читайте также
Партнерский материал
Разговоры об анализе больших данных и обо всем, что с этим ассоциируется — машинном обучении, промышленном интернете вещей и т. д., — сегодня ведутся все активнее. Несмотря на это, для оперативной производственной отчетности промышленные предприятия до сих пор зачастую используют программы для составления таблиц. Такая ситуация чаще складывается в «консервативных» отраслях, связанных с добычей полезных ископаемых (газовой, нефтяной, металлургической, химической), чем в высокотехнологичных индустриях.
Попробуем разобраться, чем это объясняется и какими решениями можно заменить устаревшие программы для составления оперативных производственных сводок на предприятиях, занимающихся добычей и переработкой ископаемых ресурсов. Для этого прежде всего следует понять, как устроена работа этих предприятий. При добыче необходимо найти, взорвать, эскалировать и перевезти необходимую горную массу, а при поточном производстве сырье проходит через трубопроводы, реакторы, смесители, сгустители и печи и превращается в полуфабрикат или готовый продукт.
Собирать информацию о том, что происходит в ходе таких процессов, сложно, а сводить ее воедино в таблице — неэффективно. Альтернативой этой программе может стать MES — Manufacturing Execution System, или система оперативного управления производством. По большому счету ее задача — наладить оперативный учет, а не в прямом смысле управлять производством. Внедрив эту систему, компания сможет собирать все измеряемые данные, поступающие от разнообразных датчиков: расходомеров, плотномеров, весов, датчиков давления, температуры и т. д. Для получения лабораторных данных, например, о содержании разных веществ, влажности, литологии, фракционном составе, в MES можно внедрить LIMS — Laboratory Information Management System, или систему управления лабораторной информацией.
Кроме того, в MES будут попадать данные из систем с уровня SCADA (диспетчерского управления и сбора данных) и АСУ ТП — автоматизированной системы управления технологическим процессом. Поскольку не всю информацию можно получить автоматически, MES предполагает также ручной ввод информации. Преимущество этой системы перед таблицей в том, что ручной ввод оставляет аудируемый след.
Задача MES — не просто сбор данных, но и их обработка, приведение к определенной логике и проверка их консистентности. Например, на поточных производствах система сводит воедино сведения о движениях и запасах сырья, полуфабрикатов и продуктов. На горнодобывающих производствах она позволяет отследить качество руды на всем жизненном цикле, от разведки до поступления на дробление и выхода готового продукта. Кроме того, MES выполняет большое количество пересчетов для перевода в общую единицу измерения — массу. Это нужно, чтобы реализовать «изюминку на торте» MES — расчет материального баланса, а в случае металлургии — баланса металлов. Этот расчет базируется на законе сохранения масс (аналогичным образом для энергобалансов используется закон сохранения энергии). Балансировка — важнейшая контрольная процедура для поточных производств. Только она позволяет обеспечить достоверность производственных данных и выявить ошибки, совершенные операторами или допущенные при использовании измерительных приборов и устаревшей информации о технологических схемах.
Почему же, если польза MES неоспорима, мы чаще слышим об успешном использовании, например, ERP, чем о внедрении системы оперативного управления производством? Я бы выделил пять основных причин.
- Отсутствие сильного заказчика. Если в случае ERP заказчик — CEO, то проект внедрения MES спускается метрологам или специалистам по ИТ и рассматривается как обычная автоматизация. При этом объем реинжиниринга процессов при внедрении MES не меньше, чем при инсталляции ERP, а влияние всех изменений на основные бизнес-процессы, возможно, даже больше.
- Отсутствие готовых универсальных ИТ-продуктов. К сожалению, решений, которые можно было бы относительно быстро и легко внедрить и которые могли бы, как ERP, диктовать логику процесса, на рынке MES нет. Как правило, на этом уровне используются продукты собственной разработки, которые не оптимизируют процессы, а встраиваются в существующие. После ухода с российского рынка западных поставщиков ПО ситуация только ухудшилась.
- Риски критической инфраструктуры. Для успешного внедрения MES необходимо собрать данные, в том числе из систем промышленного контура, что может создавать риски для критической инфраструктуры компании. Нивелирование этих рисков требует проектирования и внедрения отдельного решения на уровне «железа».
- Проблемы с оценкой совокупной стоимости владения MES. Кроме затрат на ПО и внедрение, при инсталляции MES требуются серьезные инвестиции в приборы учета, интеграцию систем АСУ ТП, выстраивание новых процессов и решение открытых методологических вопросов. Это подразумевает не только финансовые затраты, но и увеличение сроков проекта и усложняет обоснование внедрения MES.
- Неочевидная эффективность. Эффекты от использования MES менее заметны, чем, скажем, от анализа больших данных, который позволяет найти интересные зависимости и оптимизировать процессы.
В современном мире MES, безусловно, должна стать частью стратегии компании. Эта система, позволяющая хранить как сырую информацию, так и консистентную сбалансированную, может быть источником больших данных и снабжать ими остальные системы, в том числе ERP. Важным критерием успешного внедрения MES станет отказ от ведения производственной отчетности в других системах и программах.
Посчитать NPV или IRR от использования MES, наверное, невозможно. Но, как подсказывает опыт, сам процесс внедрения такого класса продуктов помогает выявить множество недостатков в производственных процессах. Эффективно внедренная MES — это цифровой двойник, позволяющий раскрыть «черный ящик» производства и увидеть истинные причины проблем, о которых многие компании даже не догадываются.
Автор: Лев Бондаренко, вице-президент по трансформации бизнеса и информатизации золотодобывающей компании «Полюс»